All categories
20
2019
-
11
Risk Assessment Report on Sudden Environmental Incidents of Chongqing Hejia Machinery Parts Manufacturing Co., Ltd. (2)
Author:
There are risks of leakage and fire during the transportation of raw materials such as guide rail oil
2.3.4 Identification of environmental risks in the transportation process:
There are risks of leakage and fire during the transportation of raw materials such as guide rail oil, recycled oil, hydraulic oil, rust-proof oil, and cutting fluid at Hejia Machinery Company. Since the transportation of oil and cutting fluids is handled by the manufacturers themselves, this evaluation does not consider environmental risks caused by transportation routes. After the manufacturer's truck enters the factory area, accidents may occur, leading to oil leakage, which could result in fire accidents if it comes into contact with a fire source.
2.3.5 Identification of secondary/associated risks:
(1) Identification of secondary/associated risks of oil fire accidents:
The main hazardous substances within Hejia Machinery Company include hydraulic oil, guide rail oil, recycled oil, rust-proof oil, cutting fluid, and sodium nitrite. When hydraulic oil, guide rail oil, recycled oil, rust-proof oil, etc., encounter strong oxidizers, open flames, or high temperatures that trigger fire accidents, combustion products include CO, smoke, and unburned hydrocarbons. Due to good ventilation conditions, there will be no significant impact on the atmospheric environment; sodium nitrite is an oxidizer that can easily ignite when in contact with reducing agents, organic matter, high temperatures, or fire sources, releasing toxic gases. The most likely location for a fire at Hejia Machinery Company is the auxiliary material storage area.
During the firefighting process of an accident, a large amount of solid waste such as dry powder, sand, and oily substances may be generated. If disposed of carelessly after the accident, it will cause secondary pollution to the environment.
(2) Identification of secondary/associated risks of oil leakage accidents:
The leakage accidents in this enterprise mainly originate from the auxiliary material storage area. Leakage from barrels storing oils may lead to a large amount of oil entering the external environment, causing environmental pollution incidents (soil, surface water, and groundwater).
2.3.6 Identification of major hazards
According to the "Technical Guidelines for Environmental Risk Assessment of Construction Enterprises" (HJ/T169-2004) and "Identification of Major Hazards in Hazardous Chemicals" (GB18218-2009); the hazardous substances involved in this enterprise's raw and auxiliary materials include guide rail oil, recycled oil, hydraulic oil, rust-proof oil, cutting fluid, and sodium nitrite. Detailed identification can be found in Table 2.3-4.
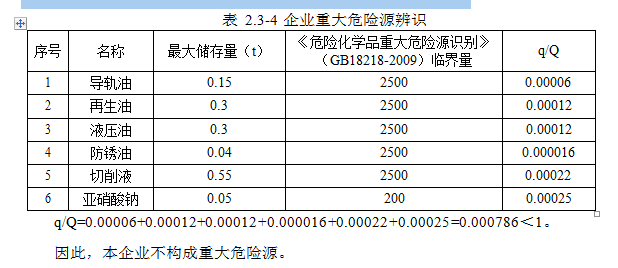
2.4 Environmental risk receptor situation around the enterprise
Environmental risk receptors are divided into atmospheric environmental risk receptors, soil environmental risk receptors, and water environmental risk receptors. Among them, atmospheric environmental risk receptors mainly include populations in key functional areas such as residential areas, medical and health facilities, cultural education institutions, scientific research units, administrative offices, important infrastructure, and enterprises; quantified by population size; soil environmental risk receptors mainly consist of basic farmland protection areas and residential commercial land around the enterprise; water environmental risk receptors mainly include drinking water source protection areas, water intake points for water plants, nature reserves, important wetlands, special ecosystems, aquaculture areas, fish and shrimp spawning grounds, and natural fishing grounds. They can be classified according to their vulnerability and sensitivity.
An investigation within a 5km radius around Hejia Machinery Company's factory boundary shows the distribution of atmospheric environmental risk receptors as shown in Appendix Figure 2.
2.4.1 Atmospheric environmental risk receptors
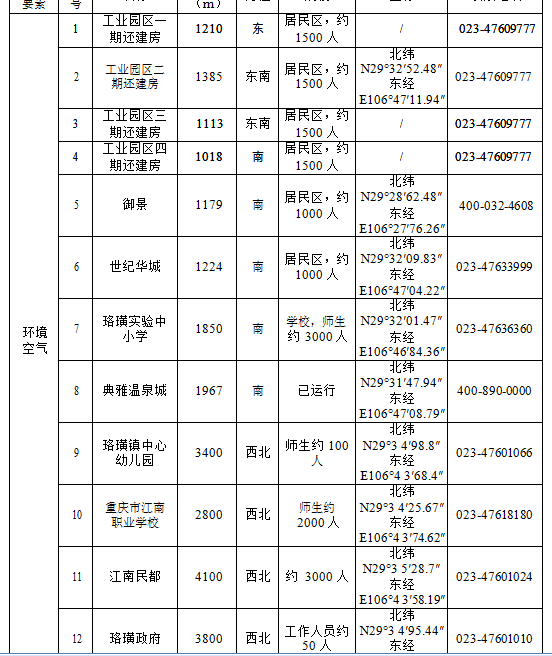
2.4.2 Soil environmental risk receptors
Hejia Machinery Company is located in Luohuang Industrial Park in Jiangjin District of Chongqing City. It belongs to an industrial concentration area with basically no farmland protection zones within a 5km radius around the production workshop; it mainly consists of industrial land and residential commercial land. The main soil environmental risk receptor is residential commercial land.
2.4.3 Water environmental risk receptors
The production wastewater from this enterprise is pre-treated by an integrated sewage treatment facility built by the company (with a treatment capacity of 5m³/d using oil separation + adjustment + mixed gas flotation + vertical flow sedimentation process) before being discharged together with domestic sewage into Chongqing Shenlu Power Machinery Co., Ltd.'s existing biochemical pool for treatment to meet the tertiary standard in the "Comprehensive Discharge Standard for Sewage" (GB8978-1996), then discharged into the sewage treatment plant in Area B of Luohuang Industrial Park for treatment to meet the first-level B standard in the "Pollutant Discharge Standards for Urban Sewage Treatment Plants" (GB18918-2002), before being released into the Yangtze River through Ganzi Creek. There are no water sources within a 3km radius upstream from the enterprise. Within a downstream range of 10 kilometers there are three drinking water source protection areas: at 6km there is Dazukou District's Yangtze River Fengshou Dam water source area and Banan District's Yangtze River Dajiang Water Plant water source area; at 9 kilometers there is Banan District's Longzhou Bay water source area.

2.5 Safety production management (excerpt from Hejia Machinery Company's self-made regulations) Chapter One: Safety precautions for loading and unloading hazardous waste
Article One: Unified command to prevent chaotic operations that may lead to accidents. Personnel involved in loading and unloading hazardous waste must strictly follow operational procedures and obey commands.
Article Two: External visitors must comply with on-site management and take appropriate safety protection measures.
Article Three: Operators should wear appropriate protective gear according to their work content based on different hazard characteristics. After completing operations, they should clean or disinfect their protective gear to ensure personal safety.
Article Four: During manual loading and unloading operations, personnel should act within their capabilities and coordinate with each other without taking risks or violating regulations.
Article Five: Loading and unloading hazardous waste should be done gently to prevent impacts, friction, vibration or dropping. Liquid iron barrel packaging should not be unloaded quickly to prevent packaging damage. Hazardous waste with damaged packaging should be moved to a safe area for repackaging.
Article Six: Hazardous waste scattered on the ground should be cleaned up promptly.
Article Seven: No eating or smoking is allowed during collection and handling operations; on-site air circulation must be maintained to prevent contamination of skin or mucous membranes. After operations are completed, hands should be washed promptly; if loading/unloading personnel experience dizziness or headaches indicating poisoning symptoms they should receive first aid according to rescue knowledge; serious cases must be sent to hospital immediately.
Article Eight: Two incompatible substances must not be collected or handled simultaneously. For heat-sensitive or moisture-sensitive materials during loading/unloading measures should be taken for heat insulation and moisture prevention.
Chapter Two: Safety precautions for flammable and explosive waste
Flammable and explosive liquids: They have a low flash point, vaporize quickly, and have high vapor pressure, making them easy to mix with air to form explosive mixtures. When the concentration in the air reaches a certain range, not only flames can cause ignition or vapor explosions, but also sparks, embers, or heated surfaces can ignite or explode them.
The following key points must be followed during collection, unloading, and handling operations:
(1) Ventilation should be conducted before loading and unloading operations in the warehouse (box);
(2) Reliable protective measures must be taken during the handling process;
(3) During loading and unloading, items must be handled gently; rolling, friction, and dragging are strictly prohibited;
(4) Transportation in summer should be arranged for early morning or late evening in cool times, and anti-slip measures should be taken during operations on rainy or snowy days. Chapter 3 Safety Precautions for Oxidizing Waste
(1) Attention should be paid to waterproofing and moisture-proofing; operations are not allowed on rainy or snowy days without rain protection facilities;
(2) If there is sweat, it should be wiped off in time; direct contact with oxidizing substances is absolutely prohibited;
(3) During loading and unloading, rolling, impact, friction, and dumping are not allowed; items must be handled gently to prevent sparks;
(4) They should be transported separately and must not be mixed with acids, organic substances, self-igniting materials, flammable materials, or items that are flammable when wet.
Chapter 4 Corrosive Waste
Corrosive waste has strong corrosiveness; it can cause damage to human bodies, animals and plants, fiber products, metals, etc., and can even cause combustion or explosions. The following key points must be followed during loading and unloading operations:
(1) Packaging containers must be strictly inspected to ensure compliance with regulations; packaging must be intact;
(2) Operators must wear appropriate protective gear;
(3) Loading and unloading must be smooth; items must be handled gently; carrying on shoulders, backs, collisions, and dropping are strictly prohibited to prevent damage to packaging;
(4) Eating and drinking during operations is strictly prohibited;
(5) Protective equipment must be cleaned thoroughly before reuse;
(6) Skin contact should be rinsed with emergency shower facilities;
(7) The loading of corrosive items should not be too high;
(8) Stacking in the air is strictly prohibited. Chapter 5 Other Hazardous Waste
Other hazardous wastes have certain toxic and harmful properties that pose certain risks to human health or the environment.
The following key points must be followed during loading and unloading operations:
(1) Packaging containers must be strictly inspected to ensure compliance with regulations; packaging must be intact;
(2) Operators must wear protective clothing, rubber gloves, rubber aprons, safety shoes, etc.;
(3) Loading and unloading must be smooth; items must be handled gently; carrying on shoulders, backs, collisions, and dropping are strictly prohibited to prevent damage to packaging;
(4) Eating and drinking during operations is strictly prohibited;
(5) Protective equipment must be cleaned thoroughly before reuse.
2.6 Current environmental risk prevention and emergency measures situation
2.6.1 Current environmental risk prevention and emergency measures situation
(1) Containment measures
--- Auxiliary material storage area: Stores hydraulic oil, guide rail oil, recycled oil, rust-proof oil and other oils as well as cutting fluids which are environmental risk substances. No containment dike is set up; the ground has no anti-seepage measures which greatly impacts the external environment.
--- Hazardous waste temporary storage room: Mainly stores waste cutting fluids and other environmental risk substances. No containment dike is set up; there are no drainage ditches or liquid collection tanks; the ground has no anti-seepage measures which greatly impacts the external environment.
--- Iron box storage area: Due to residual oils on the inner walls of iron boxes, there may be oil leakage at the iron box storage area. No containment dike is set up; the ground has no anti-seepage measures which greatly impacts the external environment.
--- Iron shavings storage area: Waste iron shavings have oil stains on their surface; they are collected using iron pallets which have a smaller impact on the external environment.
(2) Accident drainage collection measures: The company has not set up an emergency accident pool. According to the actual situation of the company, it does not need to set up an emergency accident pool. See section 3.3.3 for details.
(3) Rainwater drainage system prevention measures
The company implements rainwater and sewage diversion; the rainwater drainage system is complete.
(4) Wastewater treatment system prevention measures
The company's production wastewater is pre-treated by its self-built integrated wastewater treatment facility with a capacity of 5m³/d before entering the biochemical pool of Chongqing Shenlu Power Machinery Co., Ltd. together with domestic sewage. After reaching the tertiary standard of "Comprehensive Discharge Standard for Sewage" (GB8978-1996), it is discharged into the sewage treatment plant in Area B of Luohuang Industrial Park after reaching the first-level B standard of "Pollutant Discharge Standards for Urban Sewage Treatment Plants" (GB18918-2002), then discharged into the Yangtze River through Ganzi Creek.
(5) Implementation status of other risk prevention measures approved by environmental assessment
The company leases vacant factory buildings from Chongqing Shenlu Power Machinery Co., Ltd. for production; it mainly relies on Shenlu's factory buildings, canteen, biochemical pool on the west side of the factory area, etc.
In January 2018, Chongqing Hejia Machinery Manufacturing Co., Ltd. prepared an environmental assessment which was approved by the Environmental Protection Bureau of Jiangjin District of Chongqing on March 19, 2018; approval number: Yu (Jin) Huan Zhun [2018] No.100.
2.6.2 Analysis of the rationality of accident emergency facilities
(1) Emergency containment dike
The emergency containment dike mainly prevents leakage from oil storage devices that could lead to pollution of external environments. Auxiliary material storage area: No containment dike is set up; there are no anti-seepage measures which cannot effectively prevent oil products from flowing into external environments. Hazardous waste temporary storage room: No containment dike is set up; there are no drainage ditches or liquid collection tanks; the ground has no anti-seepage measures which greatly impacts the external environment.
--- Iron box storage area: No containment dike is set up; the ground has no anti-seepage measures which greatly impacts the external environment.
The iron filings storage area: no containment, no drainage ditch, no liquid collection tank, and no anti-seepage measures on the ground, which has a significant impact on the external environment.
(2) Accident emergency pool
The company has not set up an accident emergency pool. According to the actual situation of the company, it does not need to set up an accident emergency pool. For details, see section 3.3.3.
2.7 Current emergency materials and equipment, rescue team situation
2.7.1 Current emergency materials and equipment
According to the on-site investigation, Hejia Machinery Company's current emergency materials mainly include accident prevention facilities, accident control facilities, and facilities to reduce and eliminate accident impacts. For specific details, see Table 2.7-1.
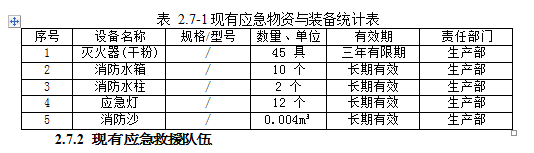
(1) Internal rescue team
During this risk assessment period, the company established internal rescue teams including an emergency rescue leadership group, a rescue and repair group, a communication liaison group, and a logistics support group, as well as an emergency office. The emergency office is mainly led by Xiao Renming from the production department (contact: 13696458843), with members including Zou Rongshui (contact: 13320352802) and Huang Wei (contact: 18983377060). They are mainly responsible for daily emergency management work, including the approval, revision, and filing of emergency plans. Office members are responsible for drafting emergency plans and assisting the office director in training and promoting knowledge related to emergency plans.
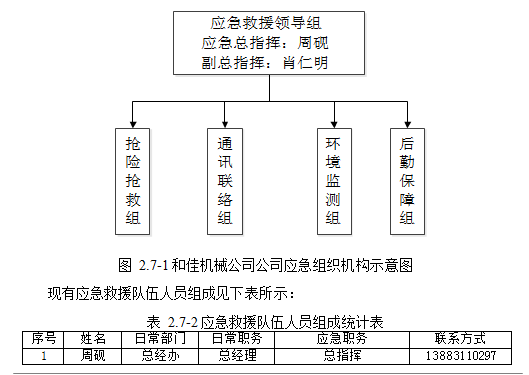
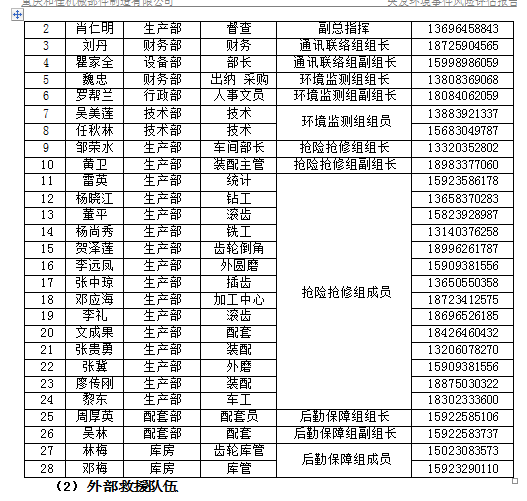
External rescue teams include the Jiangjin District Environmental Protection Bureau's emergency leadership group for sudden environmental events, emergency inspection group, emergency monitoring group, and relevant functional departments in Jiangjin District. The company has not yet signed an emergency monitoring agreement. The list of external rescue teams and contact information for surrounding enterprises can be found in Appendix 3.
2.8 Hidden dangers in the company's emergency management for sudden environmental events and risk prevention measures
Referencing the "Guidelines for Hidden Danger Investigation and Treatment of Sudden Environmental Events in Enterprises (Trial)" (Ministry of Environmental Protection Announcement No. 74 of 2016), a hidden danger investigation of emergency management and risk prevention measures was conducted for Hejia Machinery Company. See Tables 2.8-1 and 2.8-2 below.
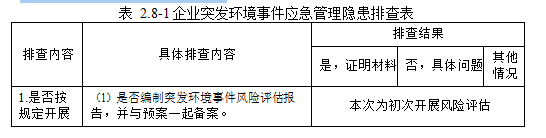
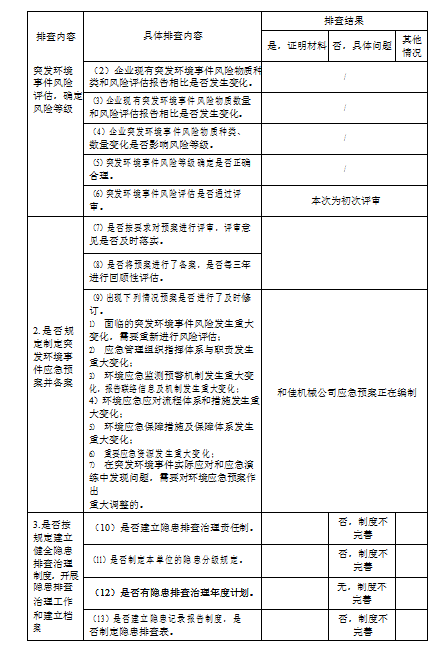
3 Analysis of Sudden Environmental Events and Their Consequences
3.1 Scenario analysis of sudden environmental events
Leaks during the processing and storage of oil products can cause pollution to water environments.
This assessment collected sudden environmental events that occurred during the use and storage of oils and sodium nitrite for comparative analysis. The list includes the following contents:
Year date, location, device scale, cause of occurrence, material leakage amount, impact range, emergency measures taken, event losses, impacts on the environment and people, etc.
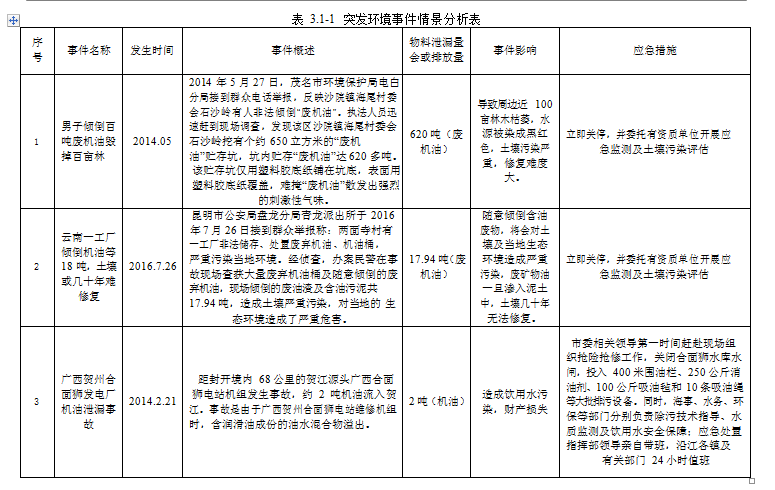
3.2 Maximum credible accidents and types
Based on on-site investigations and lessons learned from domestic sudden environmental events, the possible main types of sudden environmental events at Hejia Machinery Company include: leaks, fires, explosions, safety accidents that may cause secondary or derived environmental pollution and casualties; failure or abnormal operation of environmental risk prevention facilities; leakage incidents or traffic accidents during transportation; natural disasters, extreme weather or adverse meteorological conditions.
3.2.1 Leakage accidents
Material leaks in the tank area are mainly caused by ruptured pipelines, damaged gaskets or valves of delivery pumps due to aging or other equipment damage. The probability of leakage accidents from damaged pipelines, delivery pumps, valves, tank trucks, etc., is relatively high with an occurrence probability of about once every ten years (10^-1 times/year). The probability of small leakage accidents from storage tanks is about once every hundred years (10^-2 times/year), while major leaks leading to fires or explosions have a probability of occurring between once every thousand to ten thousand years (10^-3 to 10^-4 times/year).
/year.
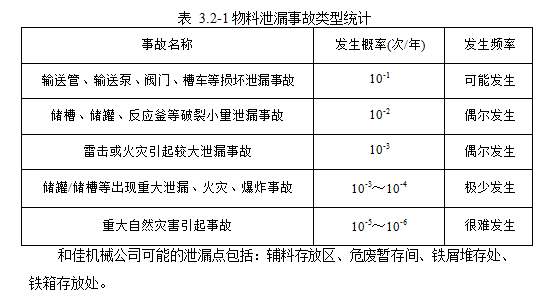
3.2.2 Fire and explosion accidents
Potential factors for fire or explosion accidents are divided into material factors and triggering factors. Material factors mainly involve the danger level of substances, material coefficients, and whether hazardous materials reach a certain scale; these are intrinsic factors for accidents. Triggering factors are external forces that lead to accidents including environmental factors, human factors, and management factors. The probability of major accidents occurring in advanced foreign chemical enterprises is between 1*10^-3 to 3.125*10^-3 times/year; the causes of fire or explosion at Hejia Machinery Company are mainly shown in Table 3.2-2.
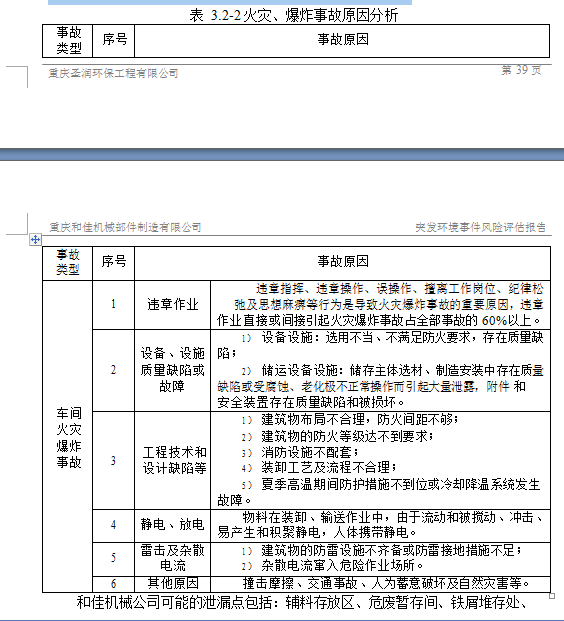
3.2.3 Environmental pollution accidents
Oil products and cutting fluids may leak during storage and production processes; if large-scale leaks occur, they may pollute surrounding air, soil, and water bodies. Sodium nitrite is an oxidizing substance that can combust or explode when encountering organic matter, reducing agents, ignition sources or high temperatures while releasing toxic and irritating nitrogen peroxide and nitrogen oxide gases.
3.3 Source strength analysis of sudden environmental event scenarios
Based on Hejia Machinery Company's operational characteristics combined with lessons learned from domestic incidents, sudden environmental events often do not occur in isolation but rather as a series of interconnected scenarios. The worst-case scenarios include:
(1) A short circuit in electrical wiring causes a fire that ignites oil products leading to combustion or even explosions resulting in material leaks; waste gases produced from combustion pollute surrounding air while oil products and firefighting wastewater directly enter the external environment causing soil and surface water pollution;
(2) Oil products encountering strong oxidizers or open flames at high temperatures during storage can lead to fire explosion incidents ultimately causing environmental pollution.
(3) Sodium nitrite is an oxidizing substance that can combust or explode when encountering organic matter, reducing agents, ignition sources or high temperatures while releasing toxic and irritating nitrogen peroxide and nitrogen oxide gases.
3.3.1 Prediction of source strength for leakage accidents in inventory areas
(1) Leakage volume calculation
The maximum storage capacity for oil products in the factory area is a total of 0.79t; therefore the maximum volume is approximately 0.88m³. The maximum storage capacity for cutting fluids is a total of 0.69t; therefore the maximum volume is approximately 0.68m³.
3.3.2 Prediction of source strength for fire explosion accidents in inventory areas
(1) TNT equivalent calculation
According to the process and the actual situation of the plant, the oils used by Hejia Machinery Company are stored at normal temperature and pressure, and there are no pressure vessels. The cutting fluid stored in the plant is generally non-flammable. Therefore, the main consideration is the oils in the plant. The maximum storage amount is 0.79t. The explosion equivalent is calculated using the vapor cloud method, and the TNT equivalent calculation formula is:
WTNT = 1.8aWf Qf / QTNT
——WTNT is the TNT equivalent of the vapor cloud, kg;
——1.8, ground explosion coefficient;
——a, TNT equivalent coefficient of the vapor cloud, take a = 0.04;
——Wf, mass of combustible substances in the vapor cloud explosion;
——Qf: heat of combustion, kJ/kg;
——QTNT, explosive energy of TNT explosives, QTNT = 4520 kJ/kg.
This assessment focuses on the auxiliary material storage area. The heat of combustion for oils is Qf = 35.9 kJ/kg, and the maximum leakage amount is 790 kg.
WTNT1 = 1.8 × 0.04 × 790 × 35.9 / 4520 = 0.45 kg
The worst-case scenario is that all combustible materials in the auxiliary material storage area burn and explode, with an explosion equivalent of
0.45 kg TNT explosives.
3.3.3 Calculation of accident wastewater volume
The volume of the emergency accident water pool to be set up is calculated using the following formula: V_total = (V1 + V2 - V3)max + V4 + V5
V1—amount of materials in the tank group or device where an accident occurs within the collection system, m3;
V2—amount of firefighting water for the tank or device where an accident occurs, m3; V2 = ∑QEliminate t,
Q消—water flow rate of firefighting facilities used simultaneously in the tank or device where an accident occurs, m3/h; teliminate—design firefighting duration corresponding to firefighting facilities, h;
V—amount of materials that can be transferred to other storage or treatment facilities during an accident, m3; V—amount of production wastewater that must still enter this collection system during an accident, m3;
V—amount of rainfall that may enter this collection system during an accident, m3; V5 = 10q•f, q = qn/n
q—rainfall intensity based on average daily rainfall, mm; qn—annual average rainfall, mm, taken as 1100 mm; n—annual average number of rainy days, taken as 120 d;
f—the catchment area for rainwater that must enter the accident wastewater collection system, ha, taken as 0.02 ha. Based on this company's situation, this time we calculate the accident pool volume based on the auxiliary material storage area.
V1—amount of materials in the tank group or device where an accident occurs within the collection system, m3; The location where this company may have a fire is in the auxiliary material storage area, with a maximum leakage volume of 0.88 m3 (see calculation process in section 3.3.1).
V2—amount of firefighting water for the tank or device where an accident occurs; if a fire occurs in the auxiliary material storage area and foam extinguishing is used with a foam supply intensity of 10 L/S for a continuous supply of 20 min. Therefore, under fire explosion conditions in the auxiliary material storage area, approximately V =12 m3 of accident foam will be generated.
V3—amount of materials that can be transferred to other storage or treatment facilities during an accident, m3; The effective volume for transferring materials in the device area is 0 m3 and effective dike volume is 15 m3.
V4—amount of production wastewater that must still enter this collection system during an accident, m3; This company has a value of 0. V5—amount of rainfall that may enter this collection system during an accident, m3;
In case of an incident in the device area, all rainwater generated must be considered to enter the emergency pool. The average annual precipitation in this area is about 1100 mm with approximately 120 rainy days per year; The catchment area for rainwater entering the accident wastewater collection system is about 200 m2; The estimated amount of rainwater entering this system is about 1.8 m3.
Thus V_total = (V + V - V)max + V + V = (0.88 +12 -0 -15) +0 +1.8 <0m3.
1 2 3 4 5
Therefore, Hejia Machinery Company does not need to set up an emergency pool.
3.4 Diffusion pathways for releasing environmental risk substances
3.4.1 Atmospheric environmental risk substance diffusion pathways
When a company experiences an environmental risk incident, environmental risk substances mainly include oils and cutting fluids used during production processes. The main affected environmental factors are ambient air, surface water, and soil.
When Hejia Machinery Company experiences a fire explosion, the waste gases produced from combustion include CO, water vapor, CO2 and hydrocarbon organic waste gases. Due to wind influence, waste gases will mainly diffuse downwind along with wind direction while hot gases from combustion diffuse into higher altitudes and surrounding atmospheric environments.
This company assumes that combustion waste gases follow a smoky plume model. The following formula is used: In assessing accident consequences, use the following plume formula:
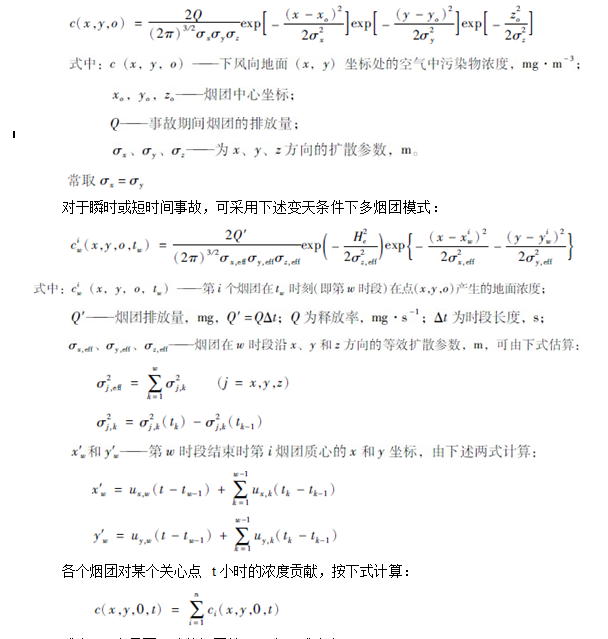
3.4.2 Diffusion Pathways of Risk Substances in Water Environment Under abnormal circumstances
2019-11-20
There are risks of leakage and fire during the transportation of raw materials such as guide rail oil
2019-11-20